صنعت فولاد ایران به عنوان یکی از ارکان اصلی توسعه اقتصادی و صنعتی کشور، امروز با بحران های متعدد و چالش های بزرگی روبروست. این صنعت که سالانه بیش از ۳۰ میلیون تن فولاد تولید می کند و در جمع ۱۰ تولیدکننده برتر جهان قرار دارد، پتانسیل قابل توجهی برای رشد و ارتقای جایگاه خود در عرصه جهانی دارد. با این حال، محدودیت های شدید در تامین انرژی، به ویژه گاز و برق، تولید و پایداری آن را به چالش کشیده است.
چالش های ناشی از بحران انرژی
بزرگ ترین چالش صنعت فولاد، بحران انرژی است. علی رغم سهم اندک فولادسازان در مصرف گاز کشور (حدود ۵ درصد)، این صنعت همواره یکی از نخستین قربانیان کمبود انرژی بوده است. در سال گذشته، حدود ۲۰ درصد از واحدهای تولید فولاد به دلیل کمبود گاز با کاهش تولید مواجه شدند و امسال نیز محدودیت های زودهنگام و شدیدتری اعمال شده است. این محدودیت ها نه تنها روند تولید فولاد را مختل کرده، بلکه موجب افزایش هزینه های تولید، کاهش صادرات و افزایش قیمت آهن آلات شده است.
کمبود گاز و برق؛ ریشه های بحران
بحران انرژی ناشی از عواملی چون زیرساخت های ناکافی، تحریم های اقتصادی و سومدیریت در بخش انرژی است. صنایع فولادی، سیمان و پتروشیمی به عنوان بزرگ ترین مصرف کنندگان انرژی، در شرایط بحرانی قرار دارند. گزارش ها حاکی از آن است که در برخی واحدهای تولیدی، مصرف گاز تا ۸۰ درصد کاهش یافته و حتی با تولید نیروگاه های اختصاصی، مشکل کمبود برق نیز به طور کامل حل نشده است. در بسیاری از موارد، این نیروگاه ها ملزم به انتقال برق به شبکه سراسری شده اند، در حالی که کارخانه ها با کمبود انرژی دست و پنجه نرم می کنند.
ناترازی انرژی در صنعت فولاد
با آغاز فصل سرما، ناترازی گاز در ایران شدت بیشتری یافته است. این در حالی است که ایران دومین دارنده منابع گاز طبیعی جهان بوده و ظرفیت تولید ۸۵۰ میلیون مترمکعب گاز در روز را دارد. اما مصرف بخش خانگی با بیش از ۴۴ درصد از کل تولید گاز، فشار زیادی بر سیستم توزیع وارد کرده و سهم صنایع و نیروگاه ها از این منابع به کمتر از ۳۰ درصد رسیده است. در نتیجه، با وجود پتانسیل بالای کشور در تولید گاز، ناترازی روزانه به حدود ۲۰۰ میلیون مترمکعب در زمستان گذشته رسید و پیش بینی می شود این رقم در سال جاری به بیش از ۲۵۰ میلیون مترمکعب برسد.
این کمبود گاز به ویژه برای صنایع حیاتی کشور نظیر فولاد و پتروشیمی مشکلات جدی ایجاد کرده است. برای مثال، کاهش تولید گاز از میدان پارس جنوبی که حدود ۷۰ درصد تامین کننده گاز کشور است، باعث کاهش تولید در این صنایع شده است. در نتیجه، برخی از واحدهای صنعتی مانند کارخانه های فولادی که پیش از این ظرفیت تولید ۳۰۰ هزار تن داشتند، اکنون با افت شدید تولید مواجه شده و تنها ۷۵ هزار تن فولاد تولید میکنند. این افت تولید نه تنها به خسارت های مالی گسترده ای در بخش های مختلف صنعتی منجر شده، بلکه باعث کاهش ارزش افزوده و اختلال در صادرات کشور نیز شده است. با توجه به این شرایط، کارشناسان پیش بینی می کنند که در سال های آینده ناترازی گاز به بیش از ۳۰۰ میلیون مترمکعب در روز برسد، که این مسئله نه تنها فشار بیشتری بر اقتصاد کشور وارد خواهد کرد، بلکه چالش های جدی برای تامین انرژی صنایع و حفظ روند تولید به وجود خواهد آورد.
چالش های صنعت فولاد ایران در رقابت جهانی
صنعت فولاد ایران علاوه بر معضل کمبود برق، با مشکلاتی چون نوسان قیمت جهانی، هزینه های بالای حمل و نقل، محدودیت های تحریمی، موانع تعرفه ای منطقه ای و مشکلات ارزی مواجه است. سیاست های چین در کاهش تولید داخلی و عرضه محصولات ارزان قیمت در بازارهای جهانی نیز شرایط را پیچیده تر کرده است.
در حالی که رقبای منطقه ای مانند ترکیه و عربستان با حمایت های دولتی و سرمایهگذاری های کلان به دنبال تثبیت جایگاه خود در بازار جهانی هستند، هزینه های تولید در ایران به دلیل ضعف زیرساخت ها و محدودیت انرژی رو به افزایش است. این وضعیت، سهم ایران از بازار جهانی را کاهش داده و تداوم آن می تواند منجر به از دست رفتن بازارهای صادراتی شود.
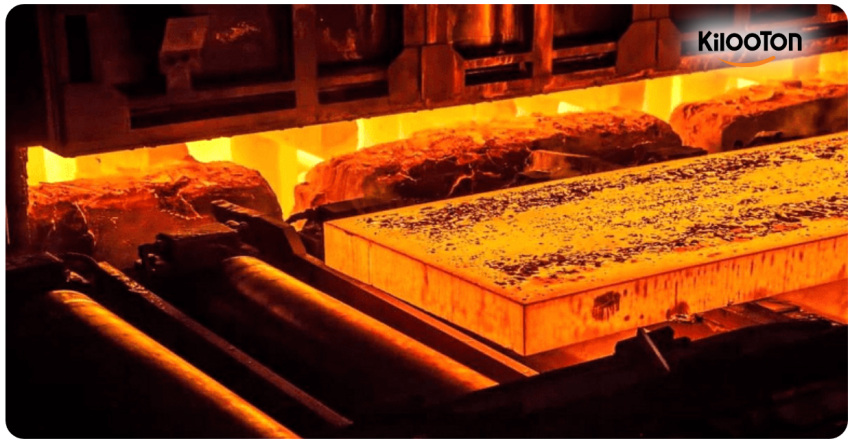
اثرات بحران بر صنعت و نیروی انسانی
کمبود انرژی تاثیرات گسترده ای بر زنجیره ارزش فولاد داشته است. از توقف تولید محصولات با ارزش افزوده بالا گرفته تا آسیب های جدی به صنایع وابسته مانند خودروسازی و ساختمان سازی. در کنار این موارد، نیروی انسانی صنعت فولاد نیز تحت فشارهای شدید روانی و مالی قرار دارد. کاهش تولید و توقف خطوط تولید منجر به تاخیر در پرداخت حقوق و کاهش انگیزه کاری شده است، به ویژه برای کارگران و کارکنان عملیاتی.
راهکارها و الزامات برای نجات صنعت فولاد
با وجود تمامی این چالش ها، صنعت فولاد ایران همچنان ظرفیت بالایی برای رشد دارد. رفع موانع اصلی، مانند تامین پایدار انرژی، می تواند به احیای این صنعت کمک کند. مهم ترین اقدامات پیشنهادی عبارتند از:
- بازنگری در سیاست های انرژی: بهینه سازی مصرف گاز و برق در صنایع و حمایت از توسعه زیرساخت های انرژی.
- حمایت از تامین تجهیزات و فناوری های پیشرفته: رفع موانع ارزی و تسهیل واردات تجهیزات کارآمد و باکیفیت.
- تقویت مدیریت بحران: تدوین برنامه های عملیاتی کوتاه مدت و راهبردی بلندمدت برای عبور از شرایط بحرانی.
- توسعه نیروگاه های اختصاصی: حمایت از سرمایه گذاری در نیروگاه های فولادی و تضمین استفاده داخلی از برق تولیدی.
- حمایت از نیروی انسانی: حفظ انگیزه و توان نیروی کار از طریق پرداخت به موقع حقوق و ارائه برنامه های آموزشی.